Operation¶
This section highlights the basic principle of operation of a Gotthard-II (GH2) module.
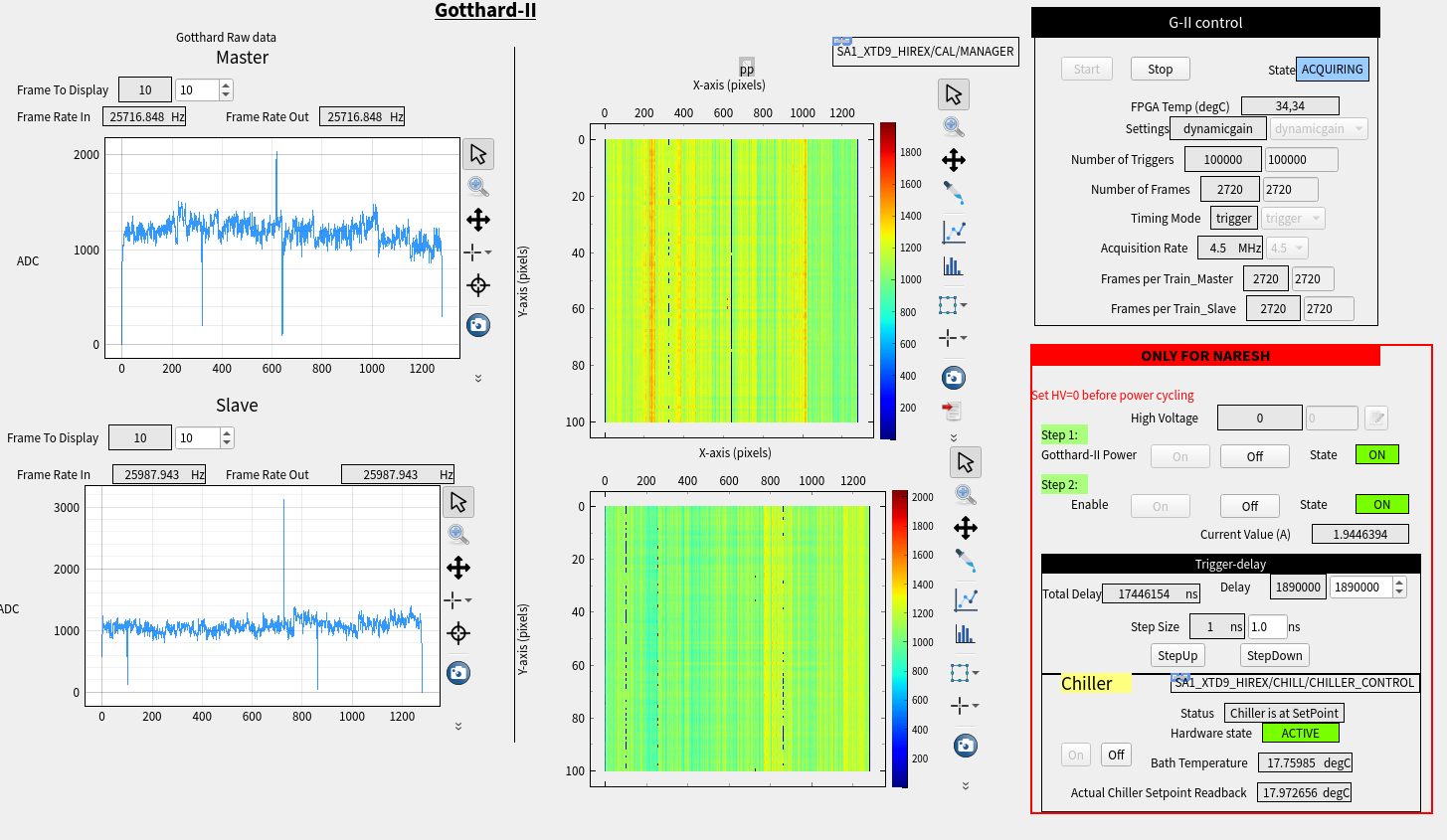
Temporary scene controlling the operation of the GH2 25 um installed in the SASE1 HIREX spectrometer.
Turning on and off¶
Cooling¶
Each module of GH2 needs cooling to dissipate the heat generated by the FEM and the GH2 readout board(s), for a total of about 12 W (for the 50 \(\mu m\) model) or 24 W (for the 25 \(\mu m\) one). Without cooling in place, the modules will heat up, operation parameters like the sensor current will not be stable, increasing the difficulty of the measurements. Moreover, there is the chance of damaging the electronics with an inefficient heat dissipation. Therefore, before powering up the modules, the cooling system must be turned on, and its correct functioning verified.
For modules in air, a set temperature above the dew point is suggested, in order to avoid possible condensation on sensitive electronic components: any temperature between 15 \(^{\circ}C\) and 20 \(^{\circ}C\) is suitable.
For the reasons explained above, operation without proper cooling is dangerous for the module.
Power¶
In order to be fully operational, the GH2 detector needs:
- a +12 V LV signal, to power the readout and control electronics and the FEM ASICs;
- an enable signal whose value must be at least +1.5 V and not higher than +12 V; this signal turns the electronics on;
- a +200 V HV signal to bias the sensor; this can be provided either by an external power supply, or with the HV module mounted on the Main Board. In this second case, the HV is set via the High Voltage property of the CONTROL device.
When powering a GH2 module it is important that the correct power procedure is being followed, otherwise the safety of the detector may be compromised.
Power Up¶
- apply the +12 V LV;
- only after, apply the enable signal: the LV needs to be already on the pin, to allow the electronics to power on in its correct state; after the enable signal is given, the detector current will start to increase: when it reaches ~1 A for the 50 \(\mu m\) , or roughly double for 25 \(\mu m\) , it is a sign that the power up is completed;
- only at this point the HV can be applied; it is however strongly suggested to first push some data from the detector, to make sure that the ASICs powered up correctly.
Power down¶
An incorrect power down is extremely dangerous for the detector: the reason is that the filtering capacitors between the sensor and the ASICs have a long discharge time. If all the power is removed simultaneously, the ASICs will power down faster than the sensor and an uncontrolled voltage at the input node is dangerous for the pixel safety. Therefore the following procedure must be followed:
- remove the HV; if using the built-in HV module, set High Voltage to zero, then wait for 10 - 15 seconds;
- remove the enable; at this point the firmware will start the power down of the electronics, starting from the ASICs, and it will be completed in few seconds (current will rapidly drop to a value close to zero);
- removing the LV is not necessary, it is however suggested to do so to put the detector in safe condition, when it will not be used for long periods of time (e.g. it is not necessary to remove it while power cycling).
Power supplies¶
There are currently three ways to provide LV and enable to a GH2 device at EuXFEL:
- via power chord; a specially adapted power chord with a power bank that transform the socket current in +12 V DC with a CC limit of at least 3 A can be used. In this case, since LV and enable would be supplied simultaneously at the respective pins, the enable must be excluded by flipping the switch in the back of the module in the OFF position: only afterwards, the power chord can be connected to the socket; a LED in the back will start to pulse green light at roughly 1 Hz; after that, the switch can be moved to the ON position, sending the enable signal to the electronics. The usage of this method is recommended only as a temporary solution;
- via MPODs; two MPOD channels can be used to provide LV and enable; a dedicated version of the powerProcedures middlelayer exists (class ID Gotthard2Power) which follows the power procedures and performs checks on the state of the High Voltage key;
- via an EuXFEL custom made power circuit coupled to LV PLC module; the module has a built-in continuity group useful
in case of sudden power cuts, and the circuit will take care of automatically removing the enable in such occurrence,
thus triggering the emergency power down procedure implemented in the detector firmware. However, the Karabo
implementation of the control devices for such power supply has not been centralized so it varies from instrument to
instrument (an example is shown in
label_hirex
); morover, the procedure and the safety checks are so far left to the operator.
Control configuration¶
The Gotthard2 CONTROL device communicates with jungfrauDetectorServer running on each module, and therefore controls the module(s) operation, by setting the acquisition parameters, and giving start and eventually stop to the acquisition. Through this device the data acquisition can be started (by clicking on the START button) and stopped (by clicking on the STOP button); the CONTROL START command has of course no impact on the DAQ and its devices, therefore if data needs to be saved, the run has to be started separately from the RUN CONTROL scene.
Basic operation settings: CONTROL device¶
Important configuration parameters that are present on the CONTROL device are listed below.
Settings: this entry sets the operation mode for the modules:
- dynamicgain: standard dynamic gain switching operation;
- fixedg1: fixed gain operation with medium gain feedback capacitance;
- fixedg2: fixed gain operation with low gain feedback capacitance;
Number of Frames: number of images acquired per train; it can be set to any value between 1 and 2720; this value has to match the Frames per Train value in the RECEIVER device;
Number of Triggers: number of trains that the detector will acquire before ending the acquisition;
Reverse Slave Read-out Mode: should be set to false for the 50 \(\mu m\) version and True for the 25 \(\mu m\) one;
There are additional parameters that can be configured, but whose operation is at the moment not supported:
- Optimize for single photon: (default: False) a boolean that if True, configures the detector with settings optimized for single photon resolution; dedicated gain calibration needs to be performed in order to properly correct raw data acquired in this mode;
- Acquisition Rate: (default: 4.5 MHz), changes the frame rate of the detector by changing the clock divider (and therefore also changing the exposure time). The only other available option is 1.1 MHz, although calibration constants are not fully available and results are in arbitrary units.
Finally, from the CONTROL device there are some parameters accessible, but they should be left to their default value:
- Additional Exposure Time: (default: 0) further increases the detector exposure time from the minimum of ~110 ns; useful only in CW mode;
- Additional Exposure Period: (default: 0)) further increases the detector exposure period from the minimum of ~222 ns; useful only in CW mode;
- Timing Mode: (default: ‘trigger’) changes the operation from external trigger (setting = ‘trigger’) to auto trigger (setting = ‘auto’);
- Timing Source: (default: external) changes the source of the acquisition trigger from external to internal and vice versa;
- Burst mode: (default: ‘burst_internal’), changes the operation mode of the detector to CW or burst with external timing.
Basic operation settings: RECEIVER device¶
- The RECEIVER devices have some operational parameters that need to be configured, especially when changing the number of
- images acquired per train:
- Frames Per Train: this parameter configures the schema of the data for the DAQ, by setting how many images per train have to be expected; this number has to be equivalent to the value of Number of Frames in the CONTROL device;
- Online Display Enable: has to be set to True to allow display of raw data directly from the RECEIVER.