Electromagnet¶
This page lists the parameters of the second version of the FFT electromagnet that was installed in the FFT end-station starting the 10th of September 2019.
Modifications¶
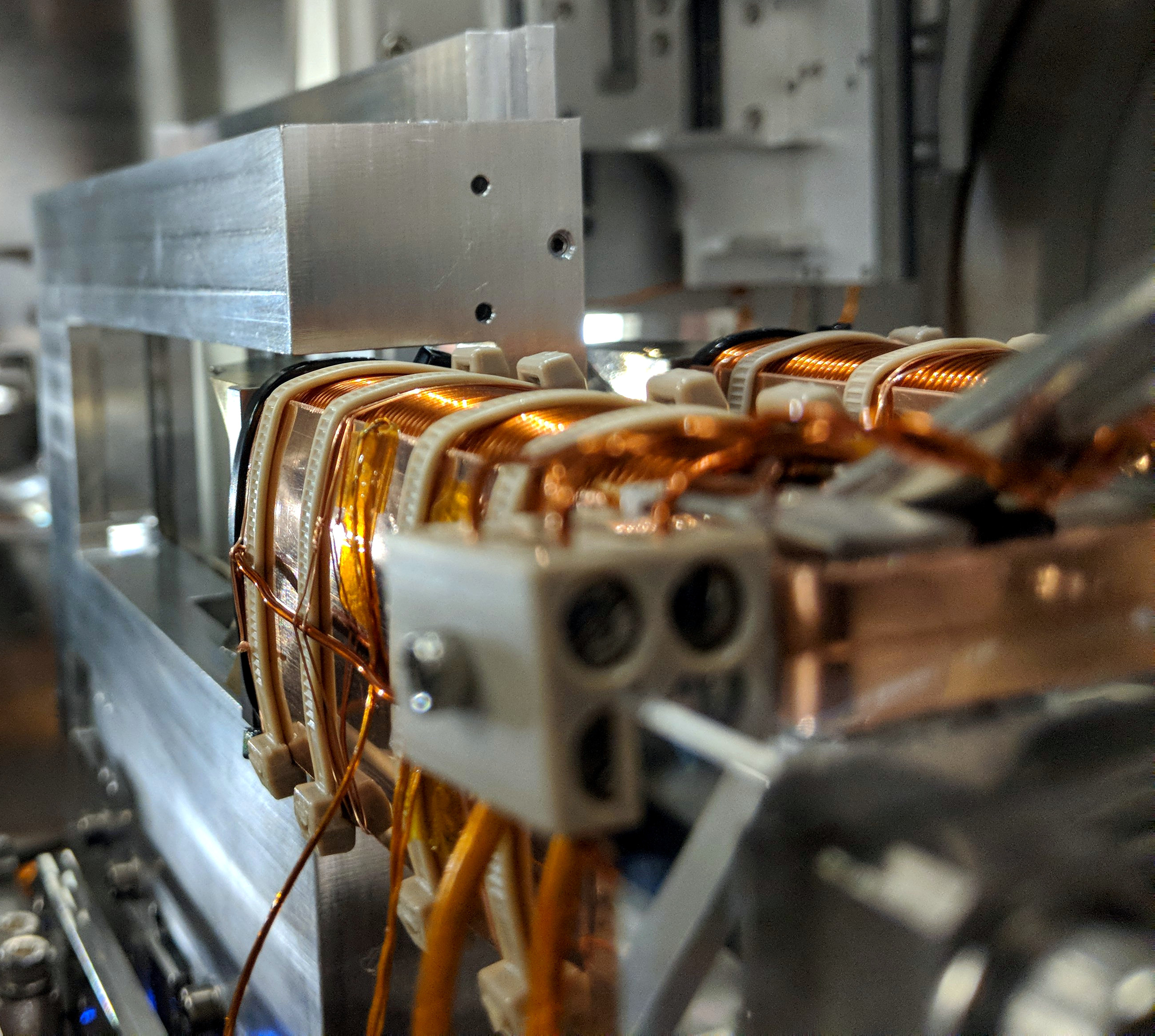
Photograph of the FFT electromagnet installed and being inserted in the Fast Solid Sample Scanner. It features copper cooling plates around the windings, a reduced gap, an additional temperature sensor embedded in the windings. From SCSelog 39.
Magnetic field¶

Magnetic field as function of current in the electromagnet. From SCSelog 56.
Current (A) | Field (mT) |
---|---|
0.0 | 0.16 |
0.5 | 32.0 |
1.0 | 60.0 |
1.5 | 93.2 |
2.0 | 121.8 |
2.5 | 155.0 |
3.0 | 185.8 |
3.5 | 218.4 |
4.0 | 249.2 |
4.5 | 274.0 |
5.0 | 296.9 |
5.5 | 318.0 |
6.0 | 335.0 |
6.5 | 349.0 |
7.0 | 359.0 |
6.5 | 350.0 |
6.0 | 336.0 |
5.5 | 318.0 |
5.0 | 298.2 |
4.5 | 274.2 |
4.0 | 247.7 |
3.5 | 217.4 |
3.0 | 186.8 |
2.5 | 155.4 |
2.0 | 120.8 |
1.5 | 92.8 |
1.0 | 61.0 |
0.5 | 27.3 |
This dependence can be fitted by:
where I is the current in A and H the field in mT.
Or, inversely, as an odd function
Small gap¶
There is another pole shoe with 3 mm gap, see https://mylog.connect.xfel.eu/#narrow/channel/380-SCS_900511_AndreasScherz/topic/Logbook/near/112691
The magnetic field is
Current (A) | Field (mT) |
---|---|
0.5 | 72 |
1 | 144 |
2 | 292 |
3 | 441 |
4 | 581 |
5 | 686 |
6 | 750 |
7 | 791 |
6 | 757 |
5 | 701 |
4 | 599 |
3 | 462 |
2 | 310 |
1 | 159 |
0 | 8 |
-1 | -142 |
-2 | -295 |
-3 | -448 |
-4 | -588 |
-5 | -689 |
-6 | -751 |
-7 | -791 |
-6 | -757 |
-5 | -701 |
-4 | -600 |
-3 | -463 |
-2 | -311 |
-1 | -160 |
0 | -9 |
The function for this is
Temperature¶
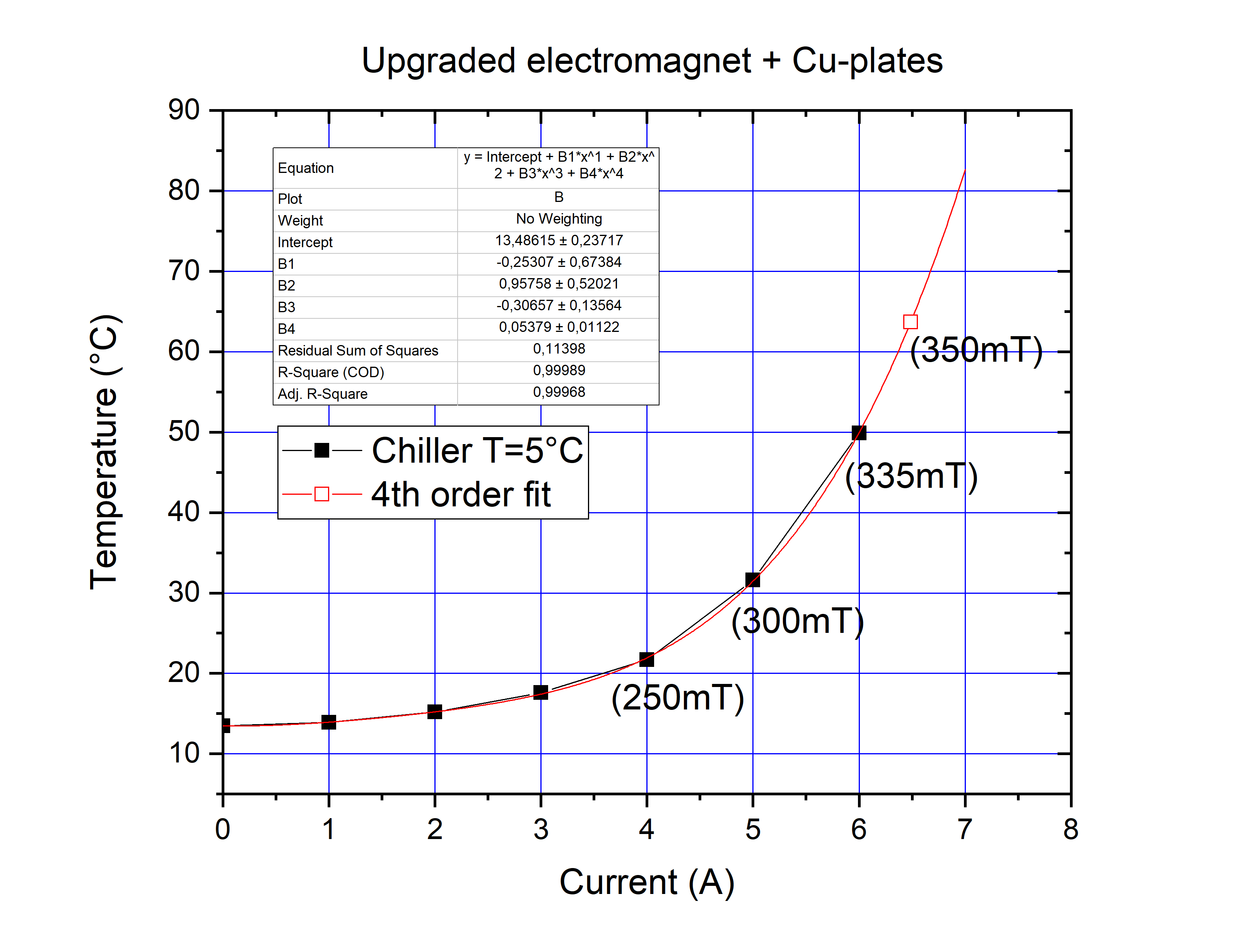
Temperature of the electromagnet for different settings. From SCSelog 90.
The temperature within the coil by the embeded thermocouple is shown in Temperature of the electromagnet for different settings. From SCSelog 90.. Combination of 5°C cooling and high water flow-rate should keep the coil temperature <70°C when operating at 7 A.
We now have two temperature sensor, a PT100 measuring the temperature on the outside of the cooling plate and a thermocouple type K measuring inside the winding.
Fast reading and writing¶
We now have a fast readout of the current applied by the Kepco via a Beckhoff analog input and we have the possibility of commanding Kepco at 10 Hz with a Beckhoff analog output.
Measurements showed that the switching between -2 and +2 A takes 8 ms and between -5 and +5 A takes 20 ms SCSelog 69.
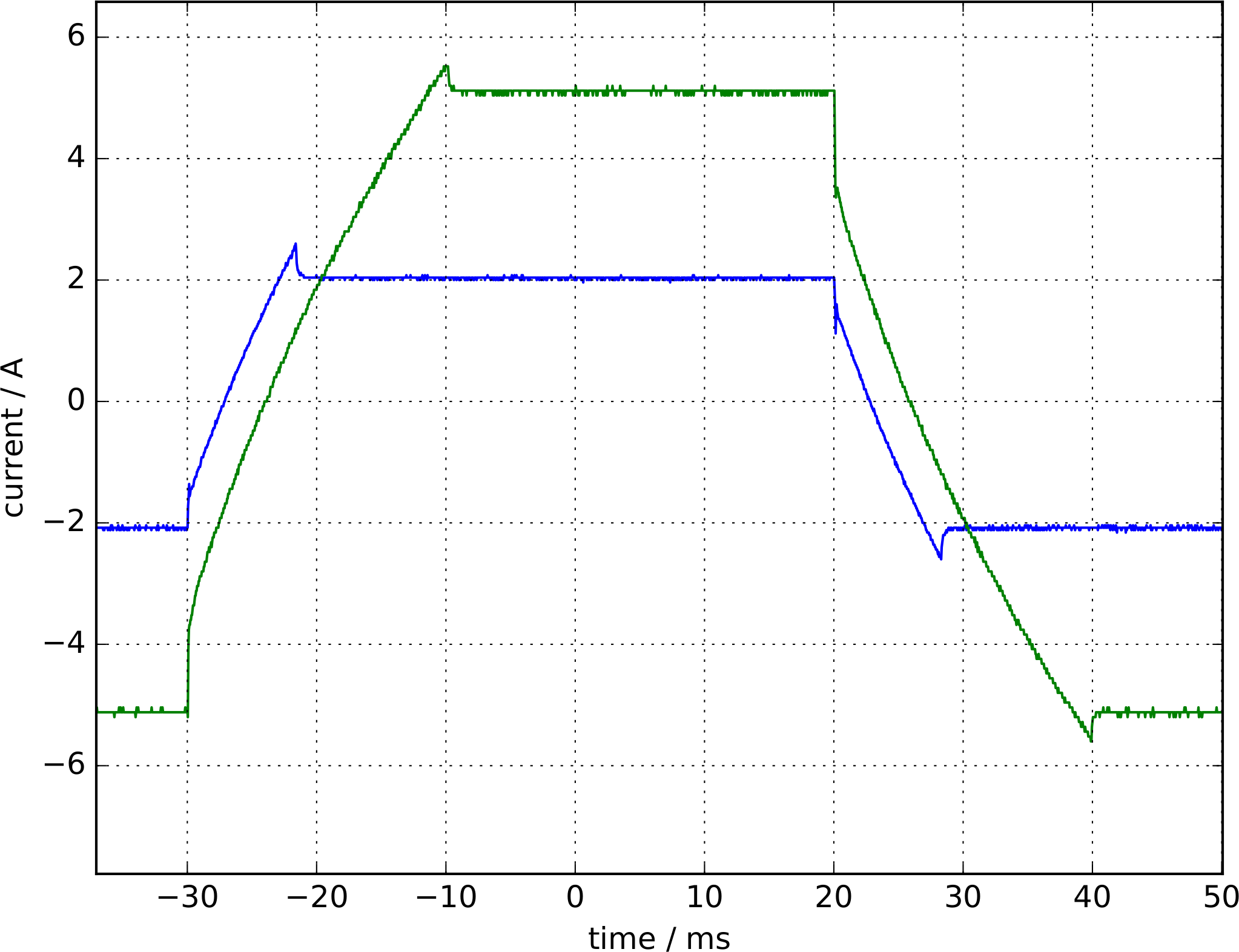
Switching from +5 A to -5 A in 20 ms. From SCSelog 69.
Electromagnet geometry¶
The gap has been reduced to 6.8 mm.
gap between pole (mm) | maximum current (A) | maximum field (T) |
---|---|---|
6.8 | 7 | 0.36 |
The geometry of the pole shoe is defined in CAD file.
Using the electromagnet¶
FFT pumped
cool magnet
Chiller power on
tap „keyboard symbol“, enter 5°C and confirm
tap „start/stop“ to start pump & cooling
check level is ok (green) and pressure is ~1.5bar
open both water valves (valves must be closed when pump is off else flood!)
chiller takes ~50 min to cool everything down
Set Kepco
Find SCS_CDIFFT_MAG/SUPPLY/CURRENT in the Karabo project
If no response from Karabo - click shutdown and reinitiate
Also try pinging via terminal:
ping exflqr14371
FUNC should be in CURR mode (by default the device starts in voltage mode which is bad), meaning current is stable and voltage is whatever it needs to be up to the set voltage limit. Voltage should thus be > 14 V (max 20 V), since we don’t want to reach the voltage limit but to be able to apply 0 to 12 A (max current) on command. Once the magnet heats up, the resistance increase and so does the voltage while the current is kept constant. In voltage mode, the current would drop at constant voltage which we are not interested.
The “Output” of the Kepco must be set to On,
Check magnet temperature is not above the respective threshold for both temperature sensors.
The magnet can be used in the scantool like a motor. It will set the current. Use this also if you want to alternate between two currents, just put the two limits into the scan tool and set two points.
Finishing routine¶
- warm up magnet - enter 24°C into chiller and confirm - wait 50 min to warm up everything - when T = 24°C, close both water valves - after the valves are closed, the chiller can be switched off
- FFT can be vented if needed
Interlocks¶
If the temperature of the electromagnet gets to high, we switch off the Kepco. This is annoying as we have to switch the Kepco back on in the rack room, but so it is.
No | Property | Op | Value |
---|---|---|---|
c1 | SCS_CDIFFT_MAG/TSENS/MAG_TEMP.Value | GT | 50 |
No | Logic | Action |
---|---|---|
a1 | c1 | COff |